Specialist Suggestions on What is Porosity in Welding and Exactly How to Resolve It
The Scientific Research Behind Porosity: A Comprehensive Overview for Welders and Fabricators
Recognizing the intricate devices behind porosity in welding is important for welders and makers aiming for impressive craftsmanship. From the structure of the base materials to the details of the welding procedure itself, a plethora of variables conspire to either worsen or alleviate the presence of porosity.
Comprehending Porosity in Welding
FIRST SENTENCE:
Assessment of porosity in welding exposes crucial understandings right into the honesty and top quality of the weld joint. Porosity, identified by the existence of tooth cavities or gaps within the weld metal, is an usual concern in welding processes. These spaces, otherwise effectively addressed, can endanger the structural honesty and mechanical homes of the weld, causing prospective failures in the finished product.

To spot and quantify porosity, non-destructive screening approaches such as ultrasonic screening or X-ray examination are usually utilized. These strategies permit the identification of inner flaws without endangering the stability of the weld. By examining the dimension, shape, and circulation of porosity within a weld, welders can make informed choices to enhance their welding procedures and attain sounder weld joints.
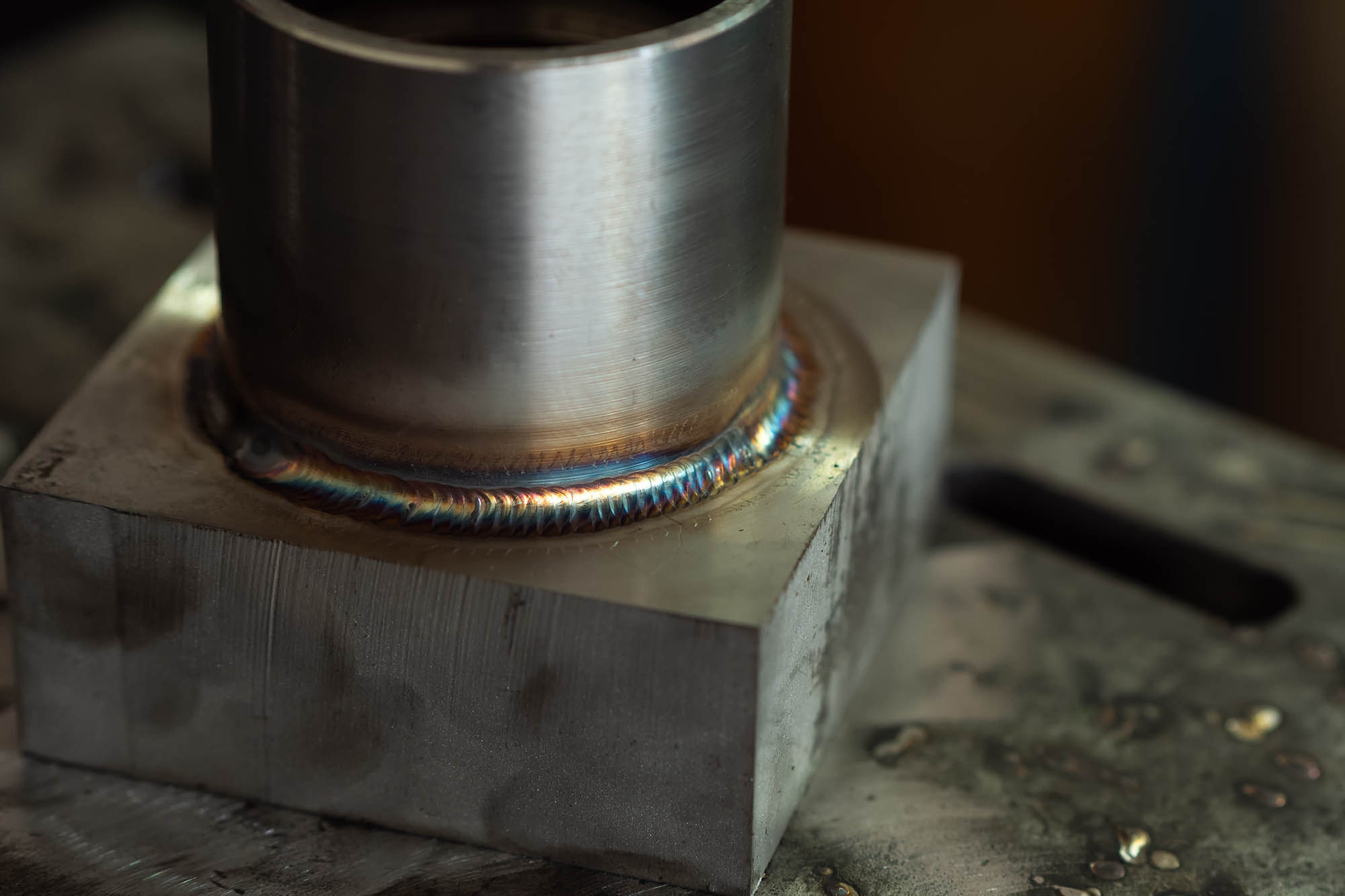
Elements Influencing Porosity Formation
The event of porosity in welding is influenced by a myriad of aspects, varying from gas securing effectiveness to the intricacies of welding parameter settings. One important factor adding to porosity development is inadequate gas protecting. When the protecting gas, normally argon or carbon dioxide, is not successfully covering the weld swimming pool, atmospheric gases like oxygen and nitrogen can pollute the molten steel, leading to porosity. In addition, the sanitation of the base materials plays a considerable duty. Pollutants such as rust, oil, or dampness can evaporate throughout welding, creating gas pockets within the weld. Welding specifications, consisting of voltage, current, travel speed, and electrode kind, likewise effect porosity formation. Making use of inappropriate settings can create too much spatter or warm input, which subsequently can cause porosity. In addition, the welding strategy employed, such as gas metal arc welding (GMAW) or protected steel arc welding (SMAW), can affect porosity development because of variations in warm distribution and gas coverage. Understanding and regulating these factors are crucial for decreasing porosity in welding procedures.
Results of Porosity on Weld High Quality
Porosity development significantly endangers next the structural stability and mechanical buildings of welded joints. When porosity is present in a weld, it produces voids or cavities within the material, decreasing the overall stamina of the joint. These spaces serve as anxiety concentration points, making the weld extra susceptible to fracturing and failing under lots. The existence of porosity likewise damages the weld's resistance to corrosion, as the entraped air or gases within deep spaces can respond with the surrounding atmosphere, resulting in deterioration over time. Additionally, porosity can hinder the weld's ability to stand up to pressure or see this influence, more jeopardizing the total quality and dependability of the welded framework. In essential applications such as aerospace, vehicle, or architectural constructions, where security and durability are critical, the destructive impacts of porosity on More about the author weld top quality can have extreme consequences, highlighting the importance of minimizing porosity with appropriate welding techniques and treatments.
Strategies to Reduce Porosity
Additionally, utilizing the suitable welding parameters, such as the appropriate voltage, existing, and take a trip speed, is important in protecting against porosity. Preserving a constant arc size and angle throughout welding additionally helps lower the chance of porosity.

In addition, picking the ideal protecting gas and preserving proper gas flow rates are necessary in minimizing porosity. Making use of the proper welding technique, such as back-stepping or employing a weaving activity, can additionally aid disperse warm uniformly and lower the possibilities of porosity development. Making sure proper air flow in the welding environment to eliminate any potential sources of contamination is important for attaining porosity-free welds. By carrying out these methods, welders can efficiently reduce porosity and generate top quality welded joints.

Advanced Solutions for Porosity Control
Executing innovative innovations and ingenious techniques plays an essential role in attaining exceptional control over porosity in welding procedures. Furthermore, using innovative welding strategies such as pulsed MIG welding or changed environment welding can likewise assist minimize porosity problems.
Another innovative service involves using advanced welding equipment. As an example, utilizing tools with built-in functions like waveform control and sophisticated power resources can boost weld high quality and minimize porosity dangers. Moreover, the implementation of automated welding systems with accurate control over parameters can substantially lessen porosity flaws.
Furthermore, incorporating innovative surveillance and examination technologies such as real-time X-ray imaging or automated ultrasonic testing can assist in discovering porosity early in the welding process, permitting prompt restorative activities. Generally, integrating these sophisticated options can significantly enhance porosity control and boost the total quality of welded elements.
Final Thought
In final thought, understanding the scientific research behind porosity in welding is important for welders and makers to generate top quality welds - What is Porosity. Advanced remedies for porosity control can even more enhance the welding process and make sure a strong and reputable weld.